EV battery plants in US anticipate boost from $2.5B federal loan
Tags
Dan Finn-Foley, energy storage expert at PA Consulting, discusses US EV battery production.
Click here to read the full Canary Media article
The article notes that the U.S. lags behind China in the capacity to build the batteries it will need to meet its growing demand for electric vehicles. The U.S. Department of Energy is planning to loan a U.S. battery manufacturing consortium $2.5 billion to help change that. DOE’s Loan Programs Office announced Monday that it has made a conditional commitment to lend the money to Ultium Cells, a joint venture of U.S. automaker General Motors and South Korean battery giant LG Energy Solutions. If approved by the DOE, the loan could help Ultium finance the battery-pack gigafactories it’s building in Michigan, Ohio and Tennessee.
It would be the first loan for battery-pack manufacturing from the Loan Programs Office’s Advanced Technology Vehicles Manufacturing loan program, which loaned a total of about $8 billion to Ford, Nissan and Tesla between 2007 and 2010. Since then, EVs have grown from a niche product to a primary focus for many automakers in the U.S. and around the world, as governments have set mandates aimed at ensuring that fossil-fueled cars, vans and trucks can be replaced with zero-emissions vehicles quickly enough to forestall the worst harms of climate change.
President Biden has set a goal for half of all U.S. auto sales to be electric or plug-in hybrid vehicles by 2030, a target that will require a massive scale-up of EVs and battery production. “Those vehicles should be, to the best of our ability, made here in the United States — and the batteries should be made here, and as many of the components as possible should be made here,” said Jigar Shah, head of DOE’s Loan Programs Office.
GM has pledged to shift to an emissions-free lineup of cars and other light-duty vehicles by 2035 and build 1 million EVs in North America by 2025, and it has committed to invest $35 billion through 2025 to hit its targets. Ultium’s battery packs are at the heart of GM’s EV strategy, as they’re designed to be interchangeably configured for a range of EVs from cars to heavy trucks.
GM plans to spend $6.5 billion at its Michigan EV factories and $2.3 billion apiece on its Ultium gigafactories in Warren, Ohio and Spring Hill, Tennessee. Those factories will have a combined annual production capacity of more than 130 gigawatt-hours of batteries when they start operations between this year and the end of 2024, Ultium spokesperson Brooke Waid said in a Monday email.
Other U.S. automakers have been catching up to GM with their domestic battery plans. Ford’s joint venture with South Korea’s SK Innovation plans to invest $11.4 billion in three battery factories and an EV assembly plant in Tennessee and Kentucky. Stellantis, the automaker formed by the merger of Fiat Chrysler and France’s Groupe PSA, has committed to a $2.5 billion battery plant in Kokomo, Indiana in partnership with South Korea’s Samsung SDI, as well as a $4.1 billion battery factory in Windsor, Ontario in partnership with LG Energy Solutions.
Will U.S.-made batteries be able to compete?
But these massive investments will only make a small dent in U.S. automakers’ dependence on batteries manufactured in Asia. China now holds a commanding lead with roughly three-fourths of global battery production, according to Benchmark Mineral Intelligence.
The U.S. and Canada together have only about 5 percent of global battery manufacturing capacity, said Dan. “If you total up all these…gigafactory announcements in the pipeline, North America only gets up to about 12 to 13 percent of the total market,” he said.
This imbalance in battery manufacturing has led to a “supply gap” for North American EV manufacturers and in the availability of North American–made EV batteries, he said. According to PA Consulting data, that supply gap stood at roughly 30 percent in 2021, with most of the batteries that automakers can’t get domestically coming from China, he said. That gap will shrink to about 12 to 13 percent by 2025 as U.S. gigafactories come online over the coming years, he said.
But as EV demand scales up dramatically, the supply gap is expected to rise to about 50 percent by 2030, Dan said. “With that big of a gap, you can expect to see a lot of [battery manufacturing] projects announced in the next two to three years.”
Whether or not North American battery production can scale up quickly enough to keep up with North American EV demand is an open question, he said. The answer will depend on factors ranging from the level of government support for the industry to whether U.S. companies can secure battery raw materials and components that are now in short supply.
In that light, DOE’s loan for the GM-LG joint venture would be “a very big deal” for Ultium, Dan said. A total of $2.5 billion “spread across three plants is a sizable chunk of the investment needed,” he said. “This shows the commitment that the U.S. has toward building out its battery infrastructure is serious, and at a meaningful scale as well.”
Even so, China’s dominance in battery manufacturing is matched by its dominance of the supply chains for the raw materials that go into modern lithium-ion batteries. This imbalance has become a hot-button issue for the Biden administration, which in March invoked the Cold War–era Defense Production Act to increase domestic production of lithium and other critical materials and minerals for EV and battery production.
Dan noted that boosting U.S. competitiveness in EVs and batteries has broad support from Republicans and Democrats alike. The $1 trillion infrastructure bill passed with bipartisan backing last year included $7.5 billion for EV charging infrastructure and more than $7 billion to expand supply chains for critical minerals needed for batteries and their components and materials, as well as $3 billion to develop next-generation battery technologies.
Ultium’s battery packs use a nickel cobalt manganese aluminum chemistry that requires about 70 percent less cobalt than the majority of lithium-ion EV batteries built on similar nickel cobalt manganese chemistries, Dan pointed out. That’s a key step in reducing the cost of Ultium batteries, and also in insulating the company from supply shortages and price spikes for the mineral.
In future years, emerging lithium-ion battery chemistries such as lower-cost lithium iron phosphate or more energy-dense solid-state batteries could well supplant today’s preferred EV technologies, he noted. Given that global battery production capacity today adds up to only about one-tenth of the total that will be needed to meet the EV targets being set by governments and automakers around the world, there’s plenty of room for new technologies to take hold.
Explore more
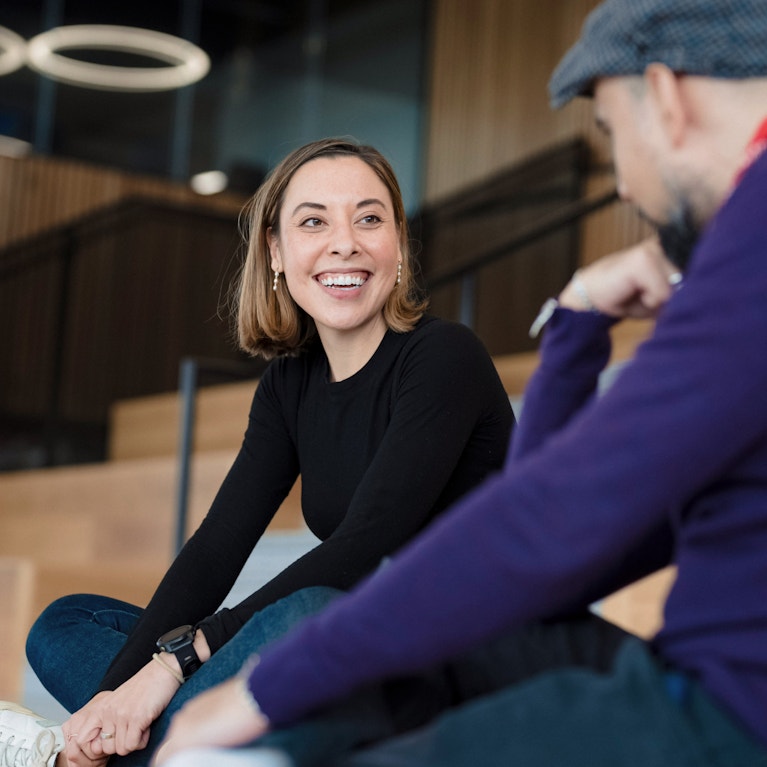