Whatever happened to the Fourth Industrial Revolution?
The past decade has seen many companies piloting so called ‘Industry 4.0’ technologies, but the lack of a clear vision of how they can help transform manufacturing across the whole business is holding up full implementation.
This article first appeared in E&T Magazine
It’s nearly ten years since Industry 4.0, also known as I4.0 or the Fourth Industrial Revolution, was first hailed as the next significant transformation in manufacturing. The digital revolution would be all-consuming, we were told, covering robotics, advanced manufacturing processes such as 3D printing and the digitisation of the factory and the supply chain.
Where are we now, as we approach the year 2020, and what does the future hold for the revolution?
Since I4.0 arrived on the scene, companies have experimented and piloted digital technologies such as AI, machine-learning and Internet of Things devices. There are many examples of these new technologies being put to good use: digital twins and digital representations of the physical manufacturing processes are being used to refine and improve existing processes, as well as to design radically different manufacturing approaches. Work by my company PA Consulting at a leading pharmaceutical manufacturer has achieved efficiency improvements of between 10 and 20 per cent by using machine learning and AI through digital representations of the physical processes.
However, very few companies, especially in the UK, have translated these into practical solutions in their factories. A recent survey by PA of smart supply chains and manufacturing found that although 99 per cent of manufacturing companies have started the digitisation journey, some 70 per cent say their plans are only at a basic or developing stage. Why have so many tested the technologies but not adopted them more widely to revolutionise their industry?
The answer seems to be that although many companies have piloted and tested different I4.0 technologies, they have not built a clear vision of how they want to use them to transform manufacturing across their business. We see pockets of success and capability, but not a transformed business. What sets the more successful companies apart is that they are systematically looking at how they roll out the technologies across their operations. As an example, a life sciences company we worked with has recently agreed a clear I4.0 vision for its supply chain and manufacturing and this is being used to focus and accelerate delivery of initiatives across the business.
Legacy IT is also becoming a consistent challenge for manufacturers whose ageing enterprise resource planning (ERP) systems cannot cope with the cloud-based digital technologies that are powering I4.0. A good example is an aerospace company which has identified that legacy ERP and manufacturing execution (MES) systems and restrictions on cloud computing are hindering rollout of I4.0 technologies. ERP vendors are waking up to this, but it has taken nearly five years for them to update their solutions and implementation is still too slow to support the agility and flexibility required. That means there is more to be done to ensure manufacturers can exploit data and systems and integrate new solutions with legacy systems so they can use their data to derive insights.
The other major challenge that organisations have faced is the availability of the people and talent needed to develop the new technologies and support the capability development of the existing workforce. The best performers have data scientists working alongside engineers and production operators to digitise the manufacturing process, but a fundamental shift in velocity will be required to train enough experts to seize the opportunities that are now opening up.
What do the next ten years hold for I4.0? We believe that many of the bedrock capabilities and technologies have been tested in organisations and that the next decade will be all about translating the promise into a fundamental transformation of manufacturing and its supply chains.
Addressing the barriers to adoption is within the grasp of manufacturing organisations, but a clear vision is needed of where they want to be in five years’ time. That means deciding whether the focus will be on driving existing performance, building connectivity across the supply chain or transforming to more agile and responsive manufacturing that is in total sync with customer needs. It will require IT departments to actively embrace cloud and digital technologies to support supply chain and manufacturing business to transform, as well as needing HR to establish effective partnerships with operations to address the talent gap.
While I4.0 progress has been slow over the last ten years, there is an argument that being late to the game may not be a bad thing. It means companies can piggyback off the testing and investment made by others, but they will need to act fast, bring the technology into the mainstream and make manufacturing an exciting and attractive career option.
Explore more
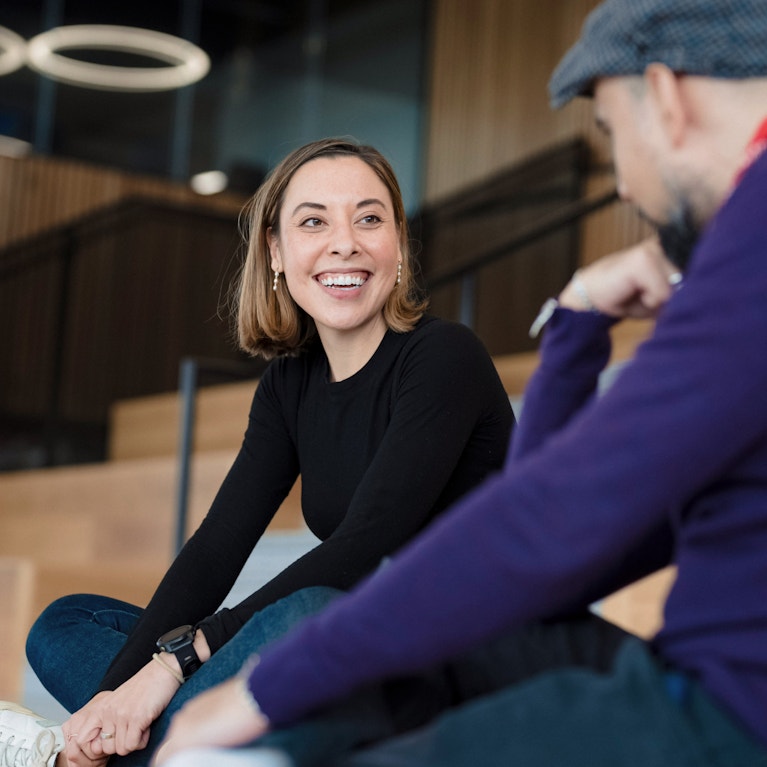